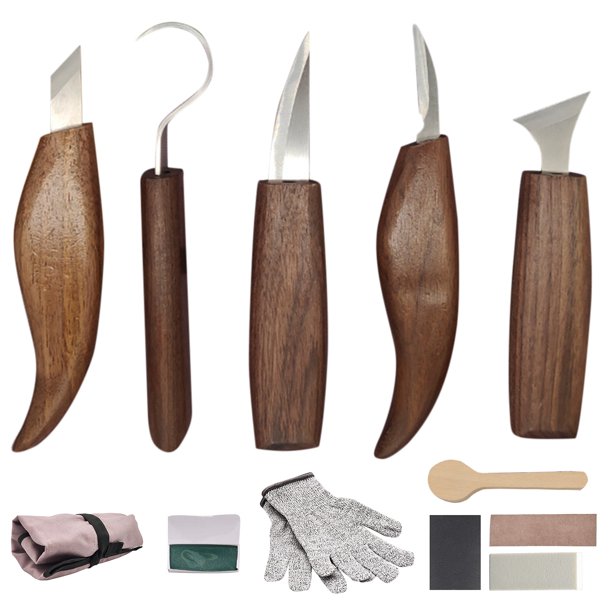
If you've ever wanted to try chip carving, then you've probably noticed that it can be a challenging task. There are many techniques and styles that you could try. But which one should you choose? What tools are you going to need? This article will share my tricks and tips for carving chips and help you choose the right one for you. There are many essentials to chip carving success, regardless of whether you prefer traditional or modern style.
Traditional
Chip carving is one form of decorative woodcarving that dates back to the beginning. You will need a straight-edged blade knife, but you can also use a skew-ground and offset knife. Chip carving is a technique that involves making small, triangular incisions into wood in order to create a pattern. This art form began over 1,000 years ago and evolved simultaneously in many different lands. Due to their widespread popularity, the designs were often very similar across nationalities making it hard to differentiate one from another.
The skills needed to carve wood became more popular as the practice spread around the globe. Chip carving is a popular method of decorating furniture in Sweden. In fact, there were even schools that taught the art. Modern chip carvers are able to benefit from the centuries-old skills and knowledge of carvers. Over the years, knowledge and experience was passed from apprentice to student. It's a lifelong process that continues today.
No cost for form
If you've always wanted to try chip carving, you've come to the right place. Murray Taylor gives you a DVD on how to create geometric and freeform carvings. This DVD is a great introductory project that provides lots of information. NTSC and English formats are available. The DVD is also available in stereo and widescreen formats. Artisan Media Ltd. is the owner of DVD. It is also available in MP4 format for Windows or Mac computers.

Geometric chip carving is based on lines, circles, triangles and circles. The technique allows for unlimited shapes and patterns and can be used to combine different styles. This method of chip carving is also called freeform chip carving. You can make your chips look beautiful in any room, no matter whether they are a flower, a dragon or a tree. The best way to incorporate different techniques into one piece is by freeform chip carving.
Techniques
Chip carving is a tradition that has existed for many centuries. Examples can be found in countless countries throughout the world. On paddles used for ceremonial purposes and boats in the South Pacific Islands, one example of chip-carving is found. The carvings were likely made using pieces of bone and seashells, although some people also used shark teeth. This book will show you how to create amazing designs by using different chip carving techniques.
If you're familiar with a few basic techniques, chip carving is very simple. First, you need to learn how to carve the fine triangular shape. This pattern is easy and straightforward to understand. To carve this pattern you will simply need to make several triangles. Then, repeat this process. But this doesn't mean you have to carve boring patterns. By changing the triangles, it is possible to create many different patterns.
Tools
Lora S. Irish will provide a free online seminar on chip carving. She teaches you how to use various carving tools and supplies, including a chip knife, stab knife, and detail bench knife. Irish also teaches you how to use different wood carving tools during this seminar. You can choose from the list below to purchase the right tool for your carving needs. You can use these tools to create simple shapes and designs, or work more intricately and make more intricate designs.
Special geometry is used to create a chip carving knife. It measures about one and a half inches in length with a narrow, curving back edge. This allows for precise incisions. A sharp point is essential to ensure that edges meet perfectly. You can also get chip carving knives made out of stainless steel. They have a sharp tip. A chip carving knife should have a sharp tip that can cut through a piece of wood.
Getting started
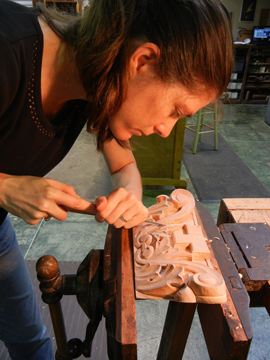
First, learn about chip carving. The process will vary depending on what type of carving you are doing. Nevertheless, you should be aware of some basic principles to ensure that your work is as accurate as possible. Chip carving is the art of cutting fine patterns in wood. To create your first chip carving, follow these steps:
Sharpening a chip carving blade is crucial. A chip carving knife's blade will have bevels at each end. This indicates that it is primary. The sharpening rock is shaped as a diamond, and can produce effective edges. It should be placed at a 10-degree angle. The stone will both sharpen and shave the chip carving knives and tool simultaneously.
FAQ
Do I need to be a genius to succeed in woodworking?
No. No. Woodworking isn't rocket science. Anyone can learn how to use basic power tools and techniques to create beautiful works of art.
How can I determine which tools are most suitable for me?
When shopping for tools, it helps to think about your needs and preferences. Do you prefer metal handles or plastic? What size nails and screws do you usually use? Are you comfortable with power tools, or would you rather use hand tools?
What material would you recommend to start learning woodworking?
Start with softwoods, such as pine or poplar. These two are the easiest to master, then you can transition to hardwood.
What's the difference?
Hobbyists like making things with wood. Professionals focus more on quality. Hobbyists usually take pride in their creations and often share them with friends and family. Before they start working on a project, professionals will spend hours researching the designs. Professionals will be meticulous about all aspects of their work, from selecting the right materials to finishing it.
Statistics
- Overall employment of woodworkers is projected to grow 8 percent from 2020 to 2030, about as fast as the average for all occupations. (bls.gov)
- Average lumber prices rose about 600 percent between April 2020 and May 2021. (familyhandyman.com)
- The best-paid 10 percent make $76,000, while the lowest-paid 10 percent make $34,000. (zippia.com)
- Most woodworkers agree that lumber moisture needs to be under 10% for building furniture. (woodandshop.com)
External Links
How To
How to make wood joints
This tutorial will help you join two pieces of wooden together. The "pocket hole joint" is a method whereby we drill holes into the wood and glue them together. This method is great if your wood's straight and smooth. You might consider dowel joinery if your wood isn’t straight or flat. These are the steps
-
Drill Pocket Hole Joints. You will need to measure and mark the exact location of your pocket hole joint. Next, drill 3/4 inch holes in each end of each piece using a handheld drilling machine or jigsaw.
-
Sand Smooth. Sanding the wood's edges will ensure that the joint doesn't split.
-
Glue Together. Apply glue to both the ends of the wood. Allow the wood to rest for five minutes before clamping it together.
-
Attach the Pieces together. After the glue has dried completely, you can clamp the pieces together until they are flush.
-
Trim Joinery. After the glue dries, trim any excess wood around your joint.
Be sure to leave enough space between each piece so that they can be turned inside-out.