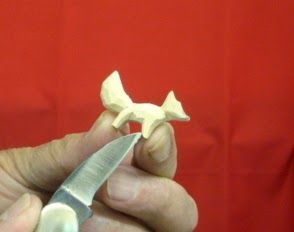
There are many types of wood carving knives available on the market. However, they all have different sizes and shapes. You should look for a knife with a thicker blade than a thin one. A knife with a curving bottom is best for slicing. A straight blade will skitter on the wood. For carving concave surfaces, a curve bottom is the best choice.
Single-blade whittling knives
You should buy a single-blade, whittling knife if you plan to carve a piece from wood. A whittling cutter is intended to cut fine details. It cannot make complicated cuts or create rough shapes. This knife is best suited for small projects. However, it will cause you to take longer time if you attempt to carve large objects.
When carving large objects such as logs or larger branches, a high-carbon steel knife is essential. It measures approximately 4.4 inches in length, making it easier to cut through larger wood and branches. Unlike a carving knife, this single-blade whittling knife comes with a leather sheath for safe storage. A limited lifetime warranty is also available for this knife.
Whittling knives made out of stainless steel
There are many different types of whitling. It is important to consider your specific needs and preferences as well as the purpose of your project. Although stainless steel knives are the most widely used, there is also a high-carbon steel knife. This steel is harder and sharpens more quickly than stainless. You should avoid using a blade that is too dull or rusted for whittling.
Carbon steel is the most common material for whittling knives. It's ideal for woodworking as it can hold a sharp edge without the need to sharpen. However, carbon steel requires frequent maintenance and rusting. Stainless Steel, however, doesn't require constant sharpening. Stainless steel whittling blades are less expensive and are rust-resistant. This material will ensure that your knife stays sharp for as long time as possible.
Wood carving knives
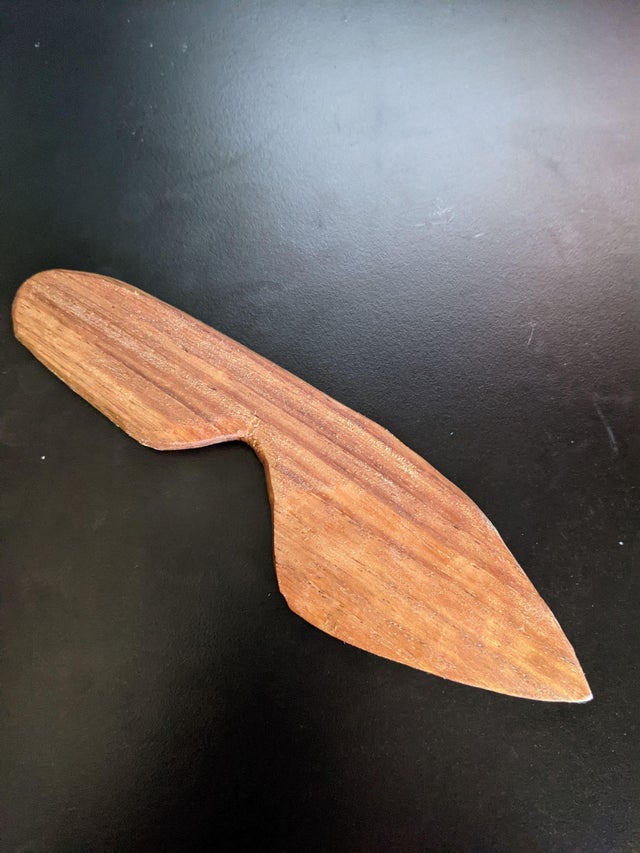
There are many types of wood carving knives. While most knives can be found in the same basic shapes and sizes as other knives, there are differences such as blade thickness. Manufacturers measure the entire blade, from tip to handle, while others measure only the cutting edge. You have the option of curved or straight bottom blades. You can use curved bottom knives for concave cutting, while straight blades will glide across wood. Here are some suggestions for selecting a carving knife.
A premium wood handle is a must-have for serious carving. A nice wood handle adds beauty and character to your carving tool. Flat handles can be uncomfortable for some people, so make sure you get a handle that is comfortable for your hands. Your hands will eventually curl around the knife's handle. An inlay can be added to a knife. It will be very easy to use a carving knife that has a nice, ergonomic handle.
Lee Ferguson wood carving knives
You will be pleased with the quality of Lee Ferguson wood carving knives, which are made with tool steel blades and rosewood handles. They are simple and elegant, but may not fit your hand. Fortunately, these knives are well-priced and can be delivered to your home for free within the USA. Lee Ferguson knives have excellent quality and are easy to sharpen. There are no shipping charges on orders over $99, either.
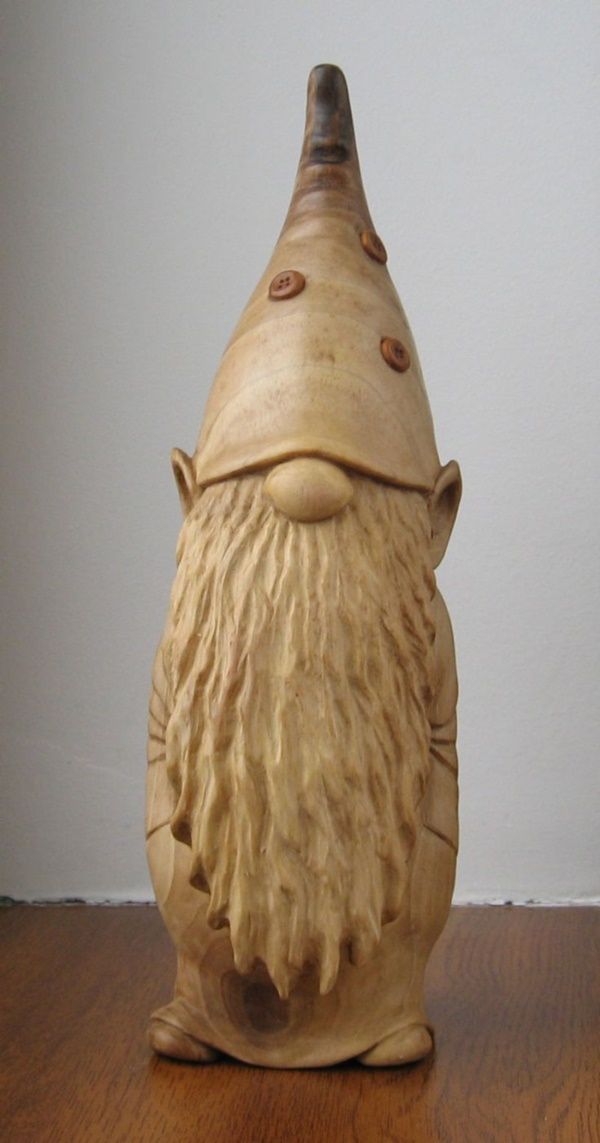
OCC tools, which are specifically designed for wood carving, come in a variety of sizes and shapes. The Flexcut is a little too large for younger whittlers. You can adjust the handle to suit smaller hands. Lee Ferguson Wood Carving Knives look great and are ready to use right out of the box. They are the perfect tool to carve wood.
FAQ
How do I identify the type of wood that I am dealing with?
Always inspect the label when buying wood. The label should detail the wood species, its moisture content and whether it has been treated or not.
What would be your first step in woodworking?
Start with softwoods, such as pine or poplar. You will feel more comfortable with these softwoods, so you can move onto hardwood.
How do you calculate woodworking prices?
The most important thing to remember when calculating costs for any project is to keep them as low as possible. It is important to ensure that you are getting the best materials prices. It is important to take into consideration all factors that can impact the cost of your projects. These include time, skill and experience. To get an idea about the average cost for common household DIY tasks, see our guide to the average woodwork project price.
What tools are best to begin with when I become a woodworker
Woodworking takes practice and patience. It takes time to learn how to use all the different tools and techniques required for woodworking.
There are many woodworking tools on the current market. Some people prefer to use power tools while others prefer manual tools.
While you have the option to pick what you like, it is essential that you get the right tool for the job. It may be a good idea to start with a basic set, if possible, if you don’t know much about hand tools.
Another option is to learn how to use a router, which is used for cutting intricate shapes into wood. These routers can be purchased at most hardware and home improvement stores.
Statistics
- Woodworkers on the lower end of that spectrum, the bottom 10% to be exact, make roughly $24,000 a year, while the top 10% makes $108,000. (zippia.com)
- In 2014, there were just over 237,000 jobs for all woodworkers, with other wood product manufacturing employing 23 percent; wood kitchen cabinets and countertop manufacturing employing 21 percent. (theartcareerproject.com)
- The U.S. Bureau of Labor Statistics (BLS) estimates that the number of jobs for woodworkers will decline by 4% between 2019 and 2029. (indeed.com)
- If your lumber isn't as dry as you would like when you purchase it (over 22% in Glen Huey's opinion…probably over 10-15% in my opinion), then it's a good idea to let it acclimate to your workshop for a couple of weeks. (woodandshop.com)
External Links
How To
How to make wooden joints
This tutorial will show how to join 2 pieces of wood together. We will be using the "pocket-hole joint", which involves drilling holes in wood and then gluing them together. This works well if the wood is straight and smooth. You might consider dowel joinery if your wood isn’t straight or flat. These are the steps
-
Drill Pocket Hole Joints. Measure and mark the location where you would like to place the pocket hole joint. With a handheld drill machine or jig saw, drill 3/4-inch deep holes in the ends of each piece.
-
Sand Smooth. You can sand the edges of the wood to ensure that it doesn't split.
-
Glue the two sides of the wood together. Apply glue to both sides of the wood. Let it sit for about 5 minutes before clamping the pieces together.
-
Fix the Pieces together. Once the glue has dried, clamp the pieces together so they are flush.
-
Trim Joinery. Trim any excess wood surrounding the joint once the glue has dried completely.
You should leave enough space between the pieces to allow you to turn them inside-out.