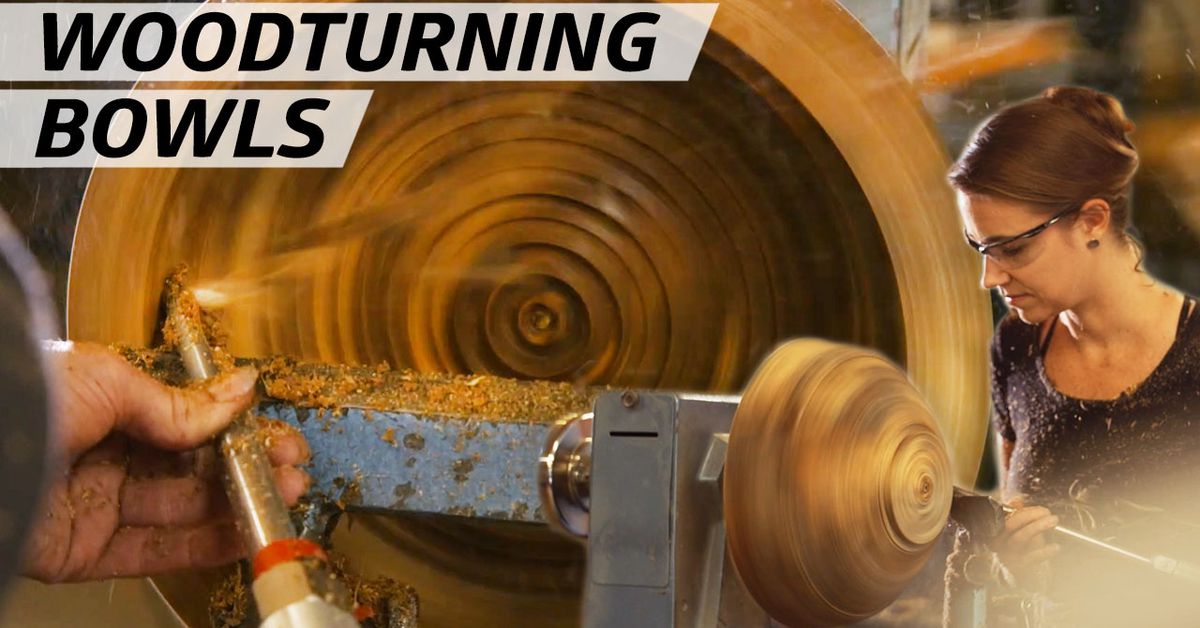
When it comes to installing a face plate, there are some basic steps to follow. These steps include selecting the right dimensions, screw diameter, and material. Once you have all these elements down, it's now time to install your faceplate. Continue reading to learn how to install your face plate. It's simple to install, and will ensure your lathe functions as intended. Listed below are the steps to installing a face plate.
Dimensions
Faceplates are a primitive accessory that can hold almost any shape and with great accuracy. Faceplates are not limited to wood. They can also be made from temporary materials or light alloys. These faceplates have a limited use and are suitable for workholding duties that require a lot of effort. The workpiece can be attached using wood screws to thread the holes on a wooden wooden faceplate. This arrangement is common in industrial lathes, but not in home workshops.
The dimensions of the faceplate are crucial. The faceplate should not be smaller than the blank. If you're planning on using it for different purposes, make sure the screws will not interfere with one another. You will also find a hole that can be used as a drill bit on the faceplate. In addition, it should have slots for a tommy bar and holes for a wrench. For each tool, it is possible to browse the faceplate.
Material
The faceplate for a lathe can be made of a variety materials, including aluminum and cast iron as well as steel and welded structures. Various materials and their properties should be considered when designing a face plate. Below are some considerations to make when selecting a faceplate material. To ensure durability and accuracy, the design process must take into account specific material properties. Cost optimization is also dependent on the materials used for a faceplate.
A faceplate for a lathe is typically made of a polymeric material and has a cylindrical surface. The faceplate is typically made from a polymeric material and has indicia lines, a plane front, and recesses that allow for the chucking of the workpiece. Some faceplates include fasteners in inserts of contrasting colors. This serves as an alert to the user in the unlikely event that a fastener falls out.
Screw size
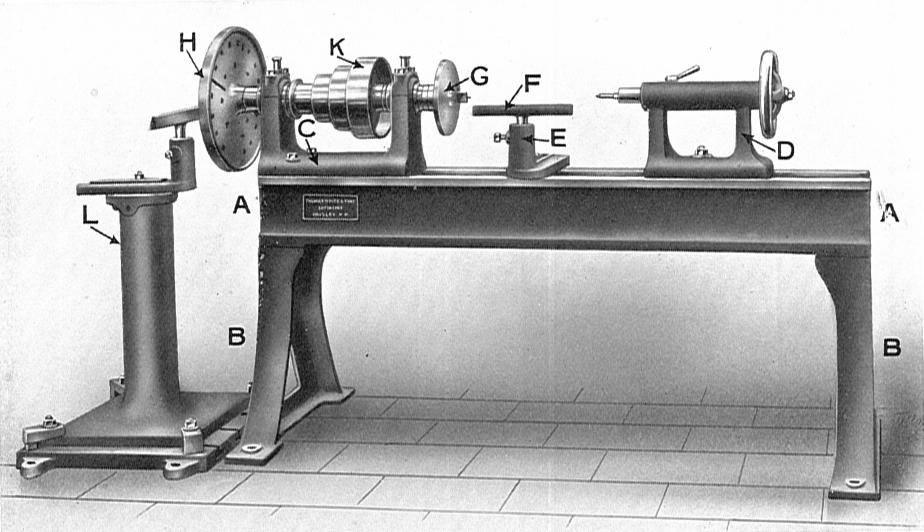
Consider using a smaller screw size if you have a wood lathe. Because the size of your screw will dictate the space that your threads can use, this is important. If you use a bigger screw diameter, the screw will protrude from the faceplate and can cause damage. Depending on your lathe's size, you may want to consider a slightly concave faceplate.
There are many options for faceplates, including steel or alloy. The smaller versions are made out of alloy while larger versions are made out of steel. Over time, the alloy faces can wear down and cause dangerous situations. Experiential turners know how to mount blanks so that they don't become too loose or prevent them from being turned. On the other hand, beginners may be too cautious with their tools or attempt to turn a blank too big for their tools.
Installation
Before you install the faceplate on your lathe make sure that the power source is turned off. Next, mount the faceplate onto your workpiece. To turn the faceplate clockwise, turn the spindle counterclockwise. Once the faceplate has been placed, engage the spindle lock. Now turn the faceplate clockwise to make it move freely. The spindle lock can be disengaged by turning counterclockwise on the lathe until the faceplate is removed.
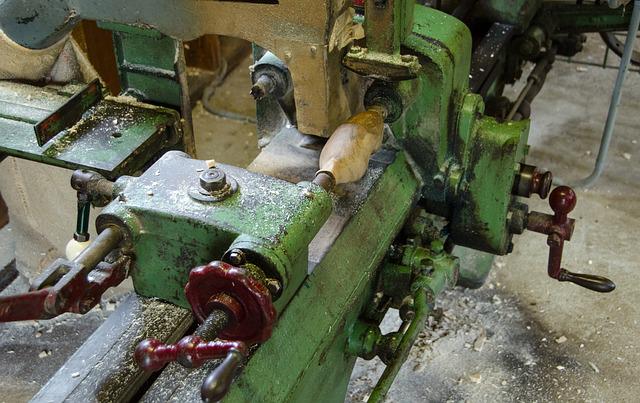
A faceplate can be described as a flat, round, and threaded plate located on the front end of a lathe. It can be used to hold clamps or other fastening items because it has a slotted surface. Once positioned on the faceplate, the workpiece is secured by sliding the clamps through the slots or screwing them directly into the faceplate's threads. Once the workpiece is in place, the faceplate can be screwed onto the lathe spindle.
FAQ
Where can you buy hardwood lumber?
Home Depot offers hardwood lumber. You can find all types of wood products at Home Depot, such as flooring, cabinets and furniture.
They also have an extensive selection of engineered hardwoods such as Ipe (Araucaria Angustifolia), Brazilian Cherry (Pau d'Arco), and Mahogany (Swietenia Macrophylla).
These woods can also be purchased online by simply searching Google for "hardwood timber"
Where do you start when it comes to woodworking?
The best way to learn how to build furniture is by building furniture. Although you will need to have tools and may make mistakes along your journey, you'll soon be able to master it.
Begin by choosing the project that you want to finish. You could make something as simple or complex as a box. Or you could build a whole entertainment center. After you have decided on a project to work on, contact a local woodworker that specializes in this type of work. Ask the local woodworker for help in deciding what tools and where to get them. Perhaps you could ask if there is someone else who does this type of work.
How can a woodworker start making money?
Many people are looking to create their own furniture and start an internet business. You don't have to sell on Etsy if your furniture is just beginning. Local craft fairs and events are great places to sell your products. A workshop could also be offered for people who are interested to learn how they can build their own furniture. Perhaps you have some experience as a carpenter/builder and would like to offer your services, such as remodeling homes and creating custom pieces.
How do I get started as a woodworker?
Woodworking is an art. It requires patience. It takes time to learn how to use all the different tools and techniques required for woodworking.
There are many different types of woodworking equipment available on the market today. Some prefer to use power tools and others prefer hand tools.
While you have the option to pick what you like, it is essential that you get the right tool for the job. Start with a basic set if you don’t have any previous experience.
You could also try learning how to use a router which is used to cut intricate shapes into wood. These tools can be purchased at most hardware stores.
Statistics
- If your lumber isn't as dry as you would like when you purchase it (over 22% in Glen Huey's opinion…probably over 10-15% in my opinion), then it's a good idea to let it acclimate to your workshop for a couple of weeks. (woodandshop.com)
- In 2014, there were just over 237,000 jobs for all woodworkers, with other wood product manufacturing employing 23 percent; wood kitchen cabinets and countertop manufacturing employing 21 percent. (theartcareerproject.com)
- Most woodworkers agree that lumber moisture needs to be under 10% for building furniture. (woodandshop.com)
- Average lumber prices rose about 600 percent between April 2020 and May 2021. (familyhandyman.com)
External Links
How To
How to properly use a saw
Hand saws can be used to cut wood into small pieces. The most common types of hand saws are circular saws, jigsaws, table saws, band saws, saber saws, crosscut saws, miter saws, and rip saws. A handsaw is a tool made of metal or plastic that cuts material like wood, plastics, metals and others.
A hand saw's main benefit is its ability make precise cuts at any angle, without the need to adjust it. It's also much easier to sharpen them than power tools. They do have their disadvantages. They are also heavy and bulky so be careful when moving them. It is possible to injure or damage your own body if the instructions are not clear.
You can hold a handsaw in many ways. When cutting, you should keep your hands away from the blades. If you don't, you might get hurt. To hold the saw properly, your thumb should be in contact with the blade. This will prevent you from accidentally touching the blade.
It is important to not put anything under the piece you are cutting when using a handheld saw. This would result in the blade slipping off the wood's surface. Before cutting, always inspect the area. Make sure no nails or screws are hidden beneath the wood.
While working with a saw, you should always use safety goggles. Safety glasses protect your eyes from dust and make it easier to see what the hand saw is doing. Safety glasses also protect your eyes from flying debris.
Before you start working with a saw, it is important to learn how to use it safely. Next, practice until your confidence is high enough to begin cutting. You'll soon be able to cut any item once you have mastered the basics.