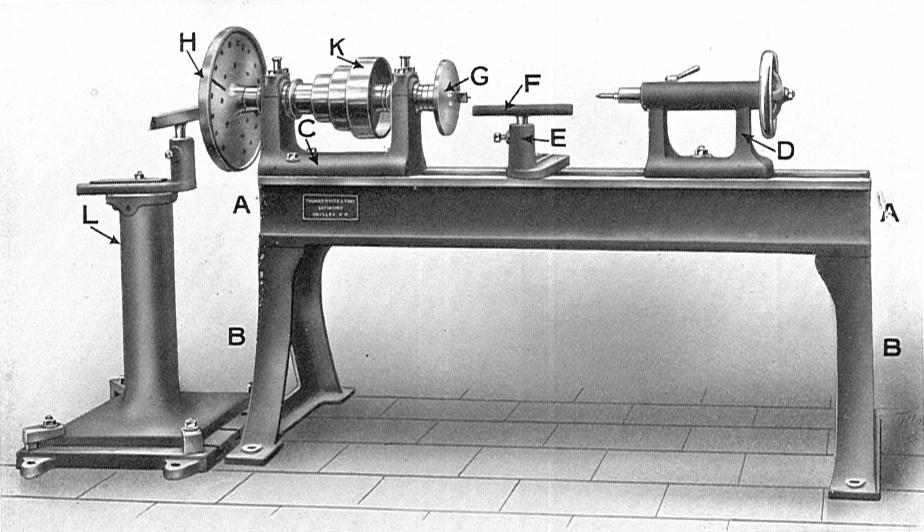
These are the steps that you need to take when installing a facial plate. These include selecting the correct dimensions, screw size, material, and how to install it. Now it is time to mount your face plate. Continue reading to find out how to install your facial plate. It is easy to install and will allow your lathe to function as it should. Here are the steps for installing a faceplate.
Dimensions
Faceplates are a primitive accessory that can hold almost any shape and with great accuracy. In addition to wood, face plates can be made from light alloys or temporary materials. These faceplates have a limited use and are suitable for workholding duties that require a lot of effort. If the faceplate is made of wooden, the workpiece can attach to it using screws. This arrangement is more popular for industrial lathes that home workshops.
Important is the dimension of your faceplate. The faceplate should be the same size as the blank you are working on. If you intend on using the faceplate for different purposes, be sure that the screws won't conflict with one another. You will also find a hole that can be used as a drill bit on the faceplate. In addition, it should have slots for a tommy bar and holes for a wrench. For each tool, it is possible to browse the faceplate.
Material
A lathe faceplate can be made from many materials, such as aluminum, cast steel, steel and welded constructions. Consider the different properties of each material when designing a faceplate. Here are some factors to consider when choosing a material for your faceplate. For accuracy and durability, it is important that the design process considers specific material properties. For cost optimization, it is also important to consider the materials that will be used on a faceplate.
A lathe faceplate is made of polymeric material. It has a cylindrical shape. It's usually designed with indicia marks, an oval front face and recesses which allow for the chucking piece. Some faceplates have fasteners located in inserts of contrasting color. This serves to warn the user if a fastener gets loose.
Screw size
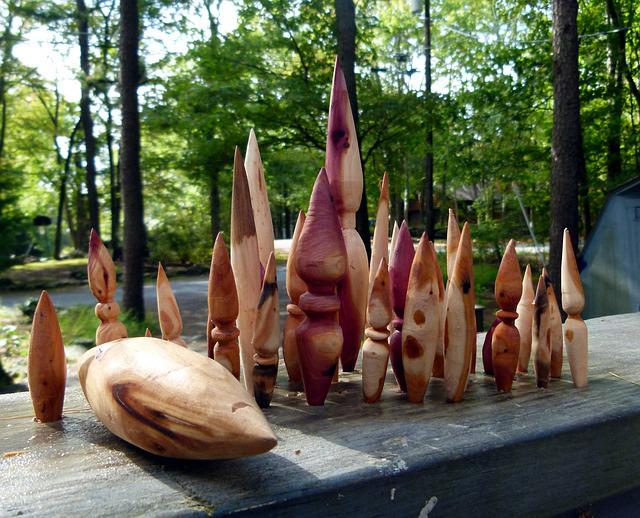
A wood lathe may require you to use a different type of screw than usual. Because your screw size will affect the space available for your threads, Your screw will be larger than the faceplate, which can cause damage to your wood bowl. Depending on the size and shape of your lathe, you might consider a slightly concave facingplate.
Faceplates are available as a variety sizes and in different materials. The smaller versions of faceplates are made from alloy while the larger ones of steel. The faces of the alloy can become damaged over time. To prevent blanks from becoming loose and prevent them from being turned, it is important that experienced turners know how mount them. Beginners, on the other hand, may use tools too close or try to turn a blank that is too large for their tools.
Installation
Before you install the faceplate on your lathe make sure that the power source is turned off. Mount the faceplate onto the workpiece. Turn the spindle clockwise to turn the faceplate. Once the plate is in its proper position, engage spindle lock. Turn the faceplate clockwise till it turns freely. To remove the faceplate turn the lathe counterclockwise, until it stops.
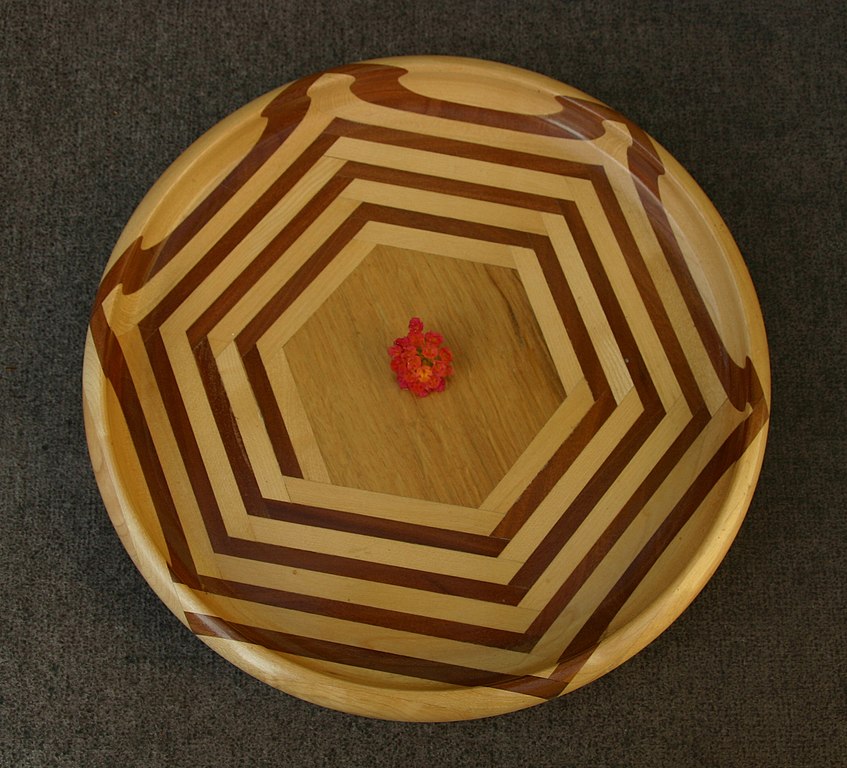
A faceplate refers to a flat round, threaded surface on the front side of a turn lathe. The slotted surface can accept clamps and any other fastening device. Once positioned on the faceplate, the workpiece is secured by sliding the clamps through the slots or screwing them directly into the faceplate's threads. After the workpiece has been placed, the faceplate is screwed on to the lathe spindle.
FAQ
How much should a skilled woodworker earn per hour?
The hourly rate of a professional woodworker depends on many factors including experience, skill level, availability, location, etc.
The average hourly rate for a skilled woodworker ranges from $20-$50 an hour.
An hourly rate of $10 for a less skilled woodworker could be possible.
Do I have the potential to make a decent living doing this?
Yes! Many woodworkers are already doing so. According to the U.S. Bureau of Labor Statistics' (BLS), in May 2012 the median annual wage of woodworkers was $34,000 This is significantly higher than the national average, which is $31,000 per year.
Where can I start woodworking?
You can learn the most effective way to build furniture by actually building it. Although you will need to have tools and may make mistakes along your journey, you'll soon be able to master it.
You should first choose the project you wish to complete. It can be as simple as a small box, or as complex as a complete entertainment center. Once you have settled on a specific project, it is time to find a woodworker in your area who is experienced in such work. Ask him or her for advice on what tools you'll need and where to find them. It's possible to ask your friend if they do this type of work.
How do I learn basic woodworking skills?
The best way to learn how furniture construction is to make your own bench. This project can easily be done using whatever wood you have at your house. If you aren't sure what type of wood to use, you can buy cheap pine boards from Lowes or Home Depot. Once you have built your bench, you will need to sand it off and then finish it with a stain/varnish.
How does a beginner woodworker earn money?
Many people want to open an online furniture business and are learning how to build it. There are other ways to make money if you're just starting out building furniture than selling on Etsy. You could also sell at craft fairs, or other local events. A workshop could also be offered for people who are interested to learn how they can build their own furniture. You might be able to offer services like remodeling homes or making custom pieces for clients if you are a skilled carpenter.
Where can I buy woodworking supplies?
There are many places you can get everything you need, and you don't have to go far. For example, you could visit local hardware stores or look online at websites like Amazon.com.
You can also look for used furniture at flea markets or garage sales.
Statistics
- In 2014, there were just over 237,000 jobs for all woodworkers, with other wood product manufacturing employing 23 percent; wood kitchen cabinets and countertop manufacturing employing 21 percent. (theartcareerproject.com)
- If your lumber isn't as dry as you would like when you purchase it (over 22% in Glen Huey's opinion…probably over 10-15% in my opinion), then it's a good idea to let it acclimate to your workshop for a couple of weeks. (woodandshop.com)
- The best-paid 10 percent make $76,000, while the lowest-paid 10 percent make $34,000. (zippia.com)
- Overall employment of woodworkers is projected to grow 8 percent from 2020 to 2030, about as fast as the average for all occupations. (bls.gov)
External Links
How To
How to join two pieces of wood together without nails
Many people love woodworking. It's fun and relaxing because you can use your hands to make something useful from wood. You may need to join two pieces without the use of nails. This article will explain how to do this so that your woodwork projects stay beautiful.
Before you can join the wood pieces together, you need to remove any rough edges. Avoid leaving sharp edges that could lead to problems later. Now you can start gluing the boards together.
If you are working with hardwood, only one side should be glue. For softwoods like cedar and pine, glue should be applied to both sides. After applying the glue, press the boards firmly until they are completely stuck together. Be sure to let the glue dry before you move on to the next step.
Once you've glued your boards together you will need to drill holes in the joints to accommodate screws. These holes will differ depending on the type and size of screw you are using. If you are going to use a half-inch wood screw, you will need to drill at least 3/4 inch deep.
Once you've drilled your holes, you'll want to drive the screws through the joint and into the backside of the board. You should be careful not to touch the board's front surface. This could cause damage. When driving the screws, try to avoid hitting the ends of the screws too much. This will help prevent splitting of the end grain.
You'll need to protect your completed project from the elements. You can either cover the entire furniture or just the top. It doesn't matter what method you use, you want something that will last many years. Examples include oil-based varnishes and polyurethanes, shellac, lacquer and others.
These products can be found in most home improvement shops. Be sure to choose the right one for your project. Also, remember that some finishes are toxic and should never be used indoors. When handling certain finishes, wear protective gear.