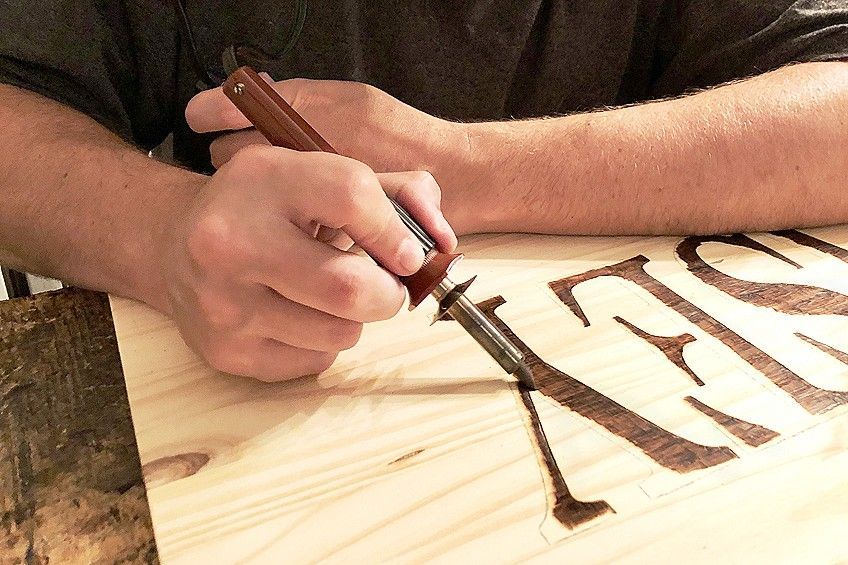
If you're a woodburning student for any length of time, chances are you've noticed how many articles you read about the latest products. Pyrography: The Art Craft of Woodburning (Magazine), Vol 6. is one of the best examples of such a trend. Publisher publishes this magazine written by Michael J. Murphy. There are several other magazines that you might want to consider reading, though.
Stuv
Stuv's 30-inch Stuv30 woodstoves come in three operating modes. The fire is visible and the stove has a refined design. Regardless of which setting you choose, you can be certain you will enjoy the experience. There are three flame patterns available, each with a distinct look to the stove. The Stuv 30 is also more efficient in heat output, providing greater warmth.
Stuv manufactures woodburning stoves and fireplaces. Its square firebox makes viewing the fire easy with its modern design. It also comes with a frameless door made of glass that won't obscure your view. You can raise or lower the glass according to your choice. You can use the fireplace fully or partially closed with its slim frame.
Phelps Pyrography
The latest issue of Phelps Pyrography woodburning magazines will provide more information about pyrography. Pyrography is a type of wood burning that uses heat to create designs on a surface. Although this art form might seem daunting at first, it is actually one of the most rewarding and fun forms of wood burning.
Pyrography is simply writing with fire. Therefore, the Greek words "pur” (or "graphos") are used to describe the term "pyrography". This practice dates back to cavemen and was known as fire needle embroidery in the Han Dynasty. The art of pyrography is a great way to experiment with different materials, and it can be used in both decorative and functional projects.
Australian Woodworker
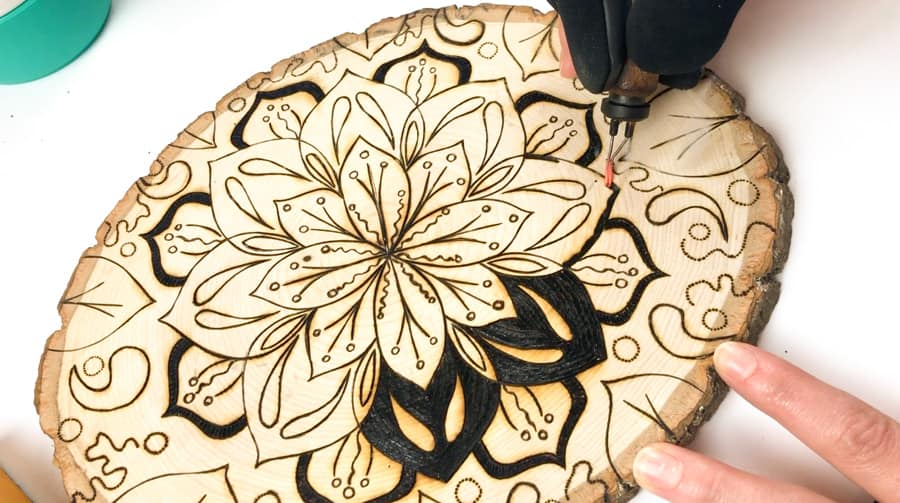
Australian Woodworker magazine is bi-monthly and covers all aspects Australian woodworking. It is the leading publication in Australia for woodworkers. It covers the latest news on both the local and international scene. It features woodcarving work by top professionals as well as talented amateur carvers.
Australian Woodworker, in addition to informative articles, features a variety of pyrographers. These include Brian Graham (an Australian Elbowlake artist), David Kreider, Deb Harding, and Francois Peters (a Belgian pyrographer). The magazine features reviews of new tools, techniques, and a detailed step-by–step guide to woodburning. Fox Chapel Publishing also publishes magazines, books and patterns.
Mauch's
Mauch was a drummer with The Ballroom Thieves from Boston one year earlier. Mauch reached out to Thoreau to tap into his inner wisdom and set off to Maine to study pyrography, which is the art of burning images into wooden boards. He found a love and passion for woodburning while on his travels.
Bowers
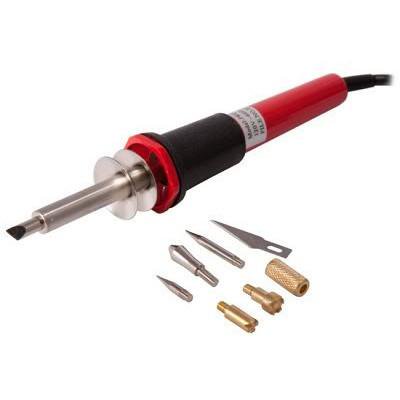
Alexandra Bowers, an artist, was featured in a Bowers woodburning issue. Bowers was raised in Scottsdale, Arizona. She grew up in a natural environment and spent her days exploring the desert outdoors with her family. This was what fuelled her passion for the craft. She has sold her items online and at Made Boutique in downtown Phoenix. She has also created a website that allows readers to learn more about her artwork.
Pyrography magazine’s annual issue can be purchased in stores, at newsstands or by mail order. Each issue includes inspiring galleries and detailed step-by–step articles, fascinating artists, and creative projects. Also included are reviews of new tools. Fox Chapel Publishing is responsible for Pyrography magazine. It also publishes books magazines and patterns. While most of the articles focus on woodworking, the magazine also covers sewing and woodworking.
FAQ
Which woods are good to use for furniture-making?
Woods are classified according their hardness. Softwoods include cedar and pine as well as cedar and cedar. They are great for outdoor furniture as they resist rot. Hardwoods include oak, maple, mahogany, and teak. Because they can't weather outside, they're usually used indoors.
What kind of wood should I use?
Oak, maple, cherry and mahogany are the most common wood types used for woodworking. Each type of wood has unique characteristics that affect the look and feel of the final product. Oak, for example, tends be darker and more hard than other woods. Birch is soft and lightweight, while mahogany is denser and heavier. You can also choose between solid wood and veneers. Veneers are thin sheets or wood that are glued together into one layer.
How do I get started as a woodworker?
Woodworking is an art. It requires patience. It takes time to learn how to use all the different tools and techniques required for woodworking.
There are many options for woodworking equipment today. Some people prefer to use power tools while others prefer manual tools.
The choice is yours, but you must ensure you choose the right tool for the job. A basic set of hand tools may be enough for you if your skills are not yet developed.
You might also consider learning how to use the router to create intricate shapes from wood. You can find these at most hardware stores.
Is it necessary to be a genius in woodworking to succeed?
No. No. Woodworking isn't rocket science. Anyone can learn how to use basic power tools and techniques to create beautiful works of art.
Are you able to teach yourself woodworking
You can learn everything best by doing. Woodworking is an art that takes patience, practice, skill and experience. To master any craft, it takes time.
You can learn the most effective way to master a skill is by actually doing it. Start small and learn from your mistakes.
Statistics
- The U.S. Bureau of Labor Statistics (BLS) estimates that the number of jobs for woodworkers will decline by 4% between 2019 and 2029. (indeed.com)
- Average lumber prices rose about 600 percent between April 2020 and May 2021. (familyhandyman.com)
- Woodworkers on the lower end of that spectrum, the bottom 10% to be exact, make roughly $24,000 a year, while the top 10% makes $108,000. (zippia.com)
- The best-paid 10 percent make $76,000, while the lowest-paid 10 percent make $34,000. (zippia.com)
External Links
How To
How to stain hardwood
Staining wood can be described as a process where chemicals are applied to the wood surface. This causes the wood to take on a new color. This chemical reaction causes the wood color to change from white and brownish red. Oak is the most commonly used wood for staining, but other woods can also be stained.
There are many ways to stain wood surfaces. Mixing the stain in a solvent such as turpentine and spraying it onto the wood is one method. Others use a solution made up of water and dye, which is then applied directly onto the wood. It is possible to mix stain into varnishes and paints, making it part of the finishing coat.
Preparing the surface for staining wood is the first step. Cleaning the wood thoroughly removes any dirt or grease that could interfere with applying the stain. Sanding the wood removes scratches and imperfections. The next step is to determine the type of stain you would like to use. There are two main types of stain: non-penetrating and penetrating. Penetrating stains penetrate deeper into the wood than non-penetrating ones, making them ideal for dark colors such as mahogany. Non-penetrating stains work best with light colors like maple.
After choosing the type and application method you prefer, gather your tools. You can use a paintbrush to apply stains. This allows you spread the liquid evenly over the surface. You should also have some handy rags to wipe up excess stains after you finish painting. If you intend to mix the stain yourself you will need enough containers to hold all the components.
After you have prepared your materials for staining, clean the area. To remove dirt and dust, use warm water and soap. You can wipe down the entire furniture using a damp rag with clean water. Be sure to get rid of all loose material, especially if staining is planned for darker wood.
The stain should be applied next. The stain can be applied by spraying or brushing the stain onto one end of the furniture. Slowly and carefully work your way along the grain to reach the opposite end. You must be careful not to allow the stain to drip off the wood's edges. Before moving on to the next steps, allow the stain drying completely.
A coat of clear polyurethane sealing agent is applied to protect the paint. Apply three coats polyurethane sealer. Let the third coat dry overnight before you sand the final coat.