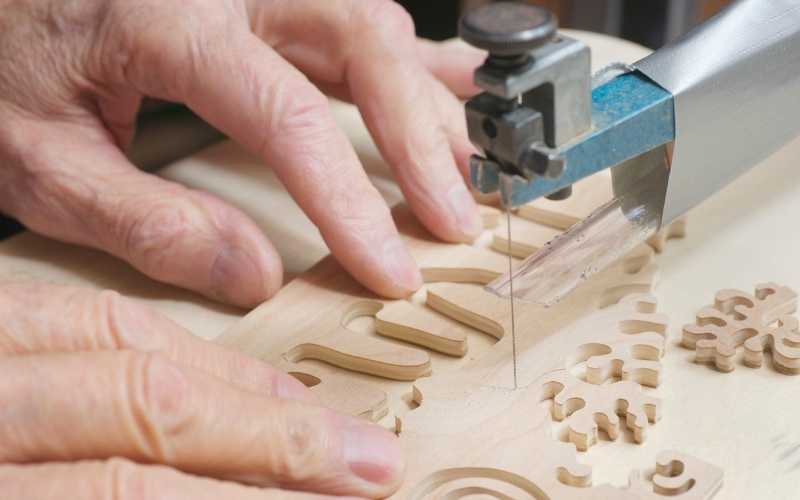
It is vital to correctly tension your bandsaw blade when you are setting it up. There are many methods involved and how they are set up will impact the end result of your cut. This guide will show you how to set up a bandsaw. You'll soon find yourself cutting. These are some tips to maximize the potential of your band saw. They are not easy to follow, but they will be worth it in time.
Use a tension tester to set up your bandsaw
To ensure the best blade tension, use a tension meter. You should carefully read the instructions before you begin cutting wood. Depending on the saw model, some of these instructions may differ slightly. The tensionwheel should be turned down one quarter to one-half turn. Once you've achieved this, you should set the blade guides to their recommended FSR.
To check the tension of your bandsaw blade, you can deflect it and listen for a sound. A tension meter can be an expensive, accurate tool that will help you adjust the blade tension for optimal blade life. While a tension meter might cost you $400 or more, it is definitely worth it. You don't have to buy a tension meter if you don't want one. A gauge can be used to check the tension of your blades.
To check the tension of your blades, use a gauge
Using a gauge when setting up a band saw is critical, as all blades require the same amount of tension to cut properly. The pulling force (generally between 200 and 800 lbs) will affect the tension. You won't get a correct reading from a tension gauge on a bandsaw if it doesn't exist. So what are you supposed to do?
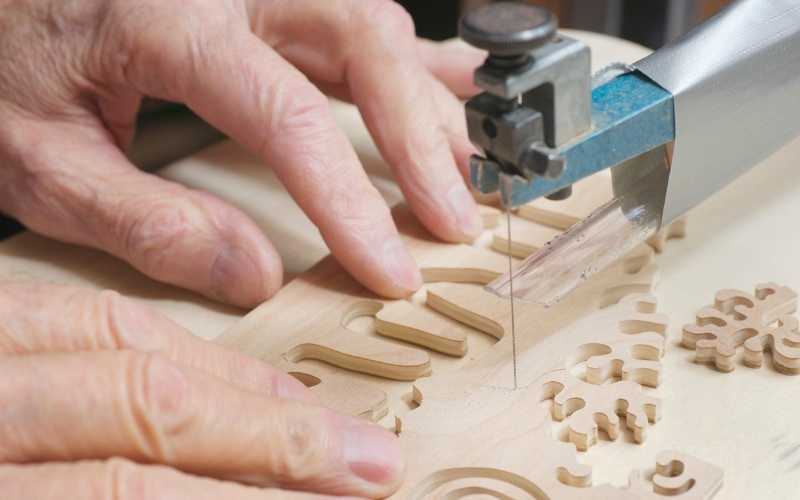
A band saw gauge is composed of two plates made from stainless steel that pivot past one another and are connected with a tensioning spring. One plate has a numeric gauge, the other a pointer indicator. The gauge clips to the blade with three pins. Two pins are on either side of your blade, and the third pin is against the blade on one.
Tracking a blade
For quality cuts, it is essential to have the right blade setup. It is essential to track the blade properly and adjust its height accordingly. Adjust the blade height so that there is approximately one-eighth - quarter-inch clearance between the material and the blade. A blade that is too low or too high will result in excessive vibration and friction, which can cause a deviation from the line. Tracking knobs can be used to stabilize wobbling knives.
First, track the blade. Ideally, the blade sits on the crown of the wheel and its deepest part lies in the center of the gullet. Next, you need to tension the blade. The tracking control is usually located at back of the saw. You should apply tension to the blade. Once the blade is in a good position, lock the control. After you are satisfied with the position of your blade, you can start cutting.
Use a long knife to reduce drift
Set up a bandsaw by placing the long blade near the center. Also, it should not be too close the wheel's rear or front edges. A blade that is less than an eighth inch from the center of the wheel is fine. However, if it touches the wheel too much, it might need to be adjusted. Adjust the fence and tilt your upper wheel to fix this.
A long blade with the same angle to your blade is the best way to account drift when setting up band saws. This will reduce drift, which refers to the material lost when the wood cutter cuts the first slice. You'll see how to correctly set the fence angle in the video. You can also duplicate the fence angle with a jig.
Using a fence to align the blade
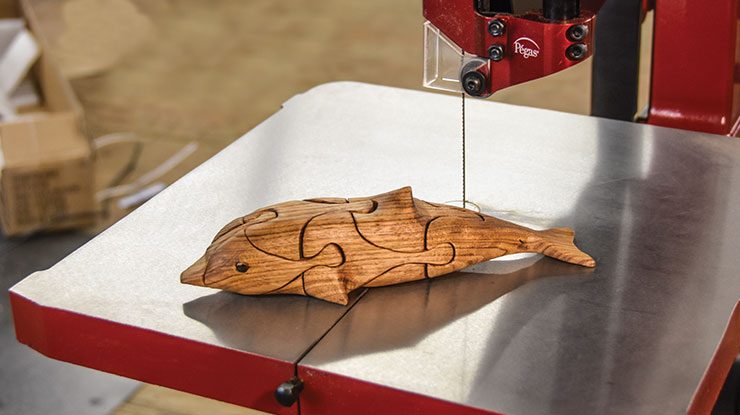
The alignment of the blade on a bandsaw is simple by using a fence. Place the fence along the fence's sidewall. Then, slide the fence over the miter slot until the face of the fence is flush with the miter slot. A finger may be used to align the blade properly.
You must first set the blade guides before you adjust the fence. You must properly set up the band saw. The fence must be placed with a sharp edge. Adjusting the fence can be done to correct any deviations in the blade. You can use a bevel square or a jig to measure the drift angle. Here's a video showing you how to do that. First determine which fence is creating drift.
FAQ
How do I organize my shop?
First, make sure you have a designated space for tools storage. To keep your tools sharp and ready for work, keep them clean of dust and debris. Hang tools and accessories using pegboard hooks.
Are you looking for tips to start a woodworking company?
It takes a lot of effort to start a woodworking business. However, if you are passionate about your hobby you will be willing to put in the effort. You'll enjoy the challenge and rewards of owning your own business.
One thing to keep in mind when launching a new venture is that you might encounter unexpected problems along the way. You might run out money, or you may have to borrow unexpectedly. Perhaps customers won't pay you as much as you had hoped. You need to be ready for these situations if you want to survive.
It is a good idea to create a separate bank account just for your company. You'll know exactly how much money is coming in by setting up a separate bank account.
How can I tell what kind of wood I am working with?
Always verify the label on wood purchases. The label should provide information about the wood species, moisture content, and whether preservatives have been used.
Where can I begin with woodworking
It is best to actually build furniture to learn how to make it. Although you will need to have tools and may make mistakes along your journey, you'll soon be able to master it.
Start by choosing a project you'd like to complete. You can make a simple box or a large entertainment center. After you have decided on a project to work on, contact a local woodworker that specializes in this type of work. Ask him or her for advice on what tools you'll need and where to find them. Perhaps you could ask if there is someone else who does this type of work.
Statistics
- Overall employment of woodworkers is projected to grow 8 percent from 2020 to 2030, about as fast as the average for all occupations. (bls.gov)
- In 2014, there were just over 237,000 jobs for all woodworkers, with other wood product manufacturing employing 23 percent; wood kitchen cabinets and countertop manufacturing employing 21 percent. (theartcareerproject.com)
- The U.S. Bureau of Labor Statistics (BLS) estimates that the number of jobs for woodworkers will decline by 4% between 2019 and 2029. (indeed.com)
- Woodworkers on the lower end of that spectrum, the bottom 10% to be exact, make roughly $24,000 a year, while the top 10% makes $108,000. (zippia.com)
External Links
How To
Tips on how to drive a nail in wood
When driving a nail into wood, it is important to first choose the correct size and kind of hammer. There are many types of hammers that you will find: claw hammers and sledgehammers; mallets; ball peen hammers; and hatchets. Each kind of hammer has its own advantages and disadvantages. A clawhammer works best when hitting something hard like nails. However, it can sometimes be difficult to see exactly where the strike is going. A sledgehammer is useful for striking large areas at once but too heavy to be effective for smaller tasks.
Place your hand flat on the side of your chosen hammer so that the handle rests in your palm. You can grip the handle with your fingers, but not so tight that it causes injury. Hold the hammer straight up, keeping your wrist relaxed. Next, swing the hammer toward the ground and aim for the nail's center. The impact of the hammer hitting the nail should be felt. You can practice swinging the hammer with a block or wood until you feel the rhythm.
You can now drive the nail by holding the hammer to your body. Place the nail so that it is perpendicular with the wood's surface. Keep your eyes focused directly on the tip of the nail. Move the hammer forward and then continue to move the hammerhead. You can repeat this several times, increasing your swing speed. After mastering the technique, you can add power to your swings. To make it more powerful, hold the hammer up high to your shoulder and then bring it down. This will allow you to exert more energy.
Once you've made the first nail hole, take out the hammer. The rest of the nails can be pulled out using a screwdriver, pry bar, or a hammer. Keep the nail heads parallel to the board's surfaces in order to avoid splitting wood.